What Is Pattern Cutting?
- Melissa
- Oct 10, 2024
- 12 min read
Updated: Dec 19, 2024
Pattern cutting is a crucial aspect of the fashion industry, playing a pivotal role in transforming design sketches into wearable garments. It's an art and science that bridges the gap between a designer’s vision and the finished product. This blog will explore the intricacies of pattern cutting, its importance in fashion, and the tools and techniques that make it an essential craft in garment production.
Table of Content

Introduction to Pattern Cutting
Pattern cutting involves creating templates that guide the cutting of fabric pieces for garments. These templates ensure that each part of a garment is accurately shaped and proportioned, which is critical for achieving a well-fitting final product. The process starts with a flat design, which is then translated into a series of shapes that can be laid out on fabric.Â
Pattern cutting requires a blend of artistic vision and technical skill. It involves precise measurements and careful calculations to ensure that the fabric pieces will come together seamlessly. Each piece must fit perfectly with the others, like pieces of a puzzle, to form the complete garment.Â
Different techniques can be used in pattern cutting, from traditional manual methods to modern digital approaches. Manual pattern cutting involves using tools like rulers, scissors, and French curves to draw and cut out pattern pieces. This method allows for hands-on adjustments and creativity but can be time-consuming.Â
On the other hand, digital pattern cutting uses specialised software to design and modify patterns. This method offers high precision and can be more efficient, especially for complex designs. It allows for easy alterations and can be saved and shared electronically, making it versatile and practical for modern garment production.
Incorporating both manual and digital techniques can provide the flexibility to achieve high-quality, bespoke clothing, combining the best of both worlds to meet diverse design needs.

The Importance of Pattern Cutting in Fashion
Pattern cutting holds a fundamental place in fashion, as it directly influences how a garment fits and presents itself. The precise cutting of patterns is essential for ensuring that garments are not only visually appealing but also comfortable and functional. A meticulously cut pattern aligns with the designer's vision, producing a garment that meets aesthetic standards while providing the necessary comfort and ease of movement.
In addition to aesthetic considerations, pattern cutting plays a crucial role in the garment's structural integrity. Properly aligned seams and accurately measured darts and pleats contribute to the durability and overall quality of the garment. This meticulous process ensures that each piece of fabric fits together perfectly, preventing issues such as misaligned seams or uncomfortable bunching.
Furthermore, pattern-cutting is instrumental in promoting sustainability within the fashion industry. By optimising the use of fabric, skilled pattern cutters can significantly reduce waste. Techniques such as zero-waste pattern cutting ensure that almost every piece of fabric is utilised, aligning with the industry's growing commitment to eco-friendly practices.
Ultimately, pattern cutting bridges the creative and technical aspects of fashion design, making it indispensable for producing high-quality, well-fitting garments that stand the test of time.

Historical Background of Pattern Cutting
Pattern cutting has a rich history, evolving from ancient garment-making techniques to the sophisticated methods used today. In its earliest forms, clothing was made by draping and stitching fabric directly onto the body or dress forms. This method was intuitive but lacked the precision and consistency needed for complex designs.
The 19th century marked a significant turning point with the advent of paper patterns. This innovation revolutionised the fashion industry, facilitating mass production and the standardisation of sizes. These paper patterns enabled tailors and dressmakers to create garments with a higher degree of accuracy and repeatability.
As fashion continued to evolve, so did the tools and techniques used in pattern cutting. The Industrial Revolution brought advancements in sewing machines and fabric production, further refining the art of pattern cutting. This era saw the introduction of more structured and tailored garments, necessitating precise pattern work.
In the mid-20th century, the rise of haute couture highlighted the importance of skilled pattern cutters. These professionals were revered for their ability to translate the intricate designs of top fashion houses into wearable art.
Today, the blend of traditional methods and digital technology has pushed the boundaries of what is possible in pattern cutting. From the tactile experience of manual pattern-making to the high-tech precision of digital software, the craft continues to be a cornerstone of garment production, embodying both heritage and innovation.

Key Elements of a Pattern
Patterns consist of several crucial components that contribute to the final garment's shape and structure. Darts are essential for adding three-dimensional form to flat fabric, allowing it to contour elegantly to the body's curves. These small, tapered folds are particularly vital in achieving a tailored fit in areas like the bust, waist, and hips.Â
Pleats are another key element, serving both functional and decorative purposes. They create fullness and movement in skirts, dresses, and trousers, adding a dynamic aspect to the garment. Pleats can be simple or intricate, depending on the desired aesthetic and the garment's design.
Seams are where the different pieces of fabric are stitched together, forming the garment. The accuracy of seams is paramount, as it affects both the fit and durability of the clothing. Properly aligned seams ensure a polished, professional look and enhance the garment's structural integrity.
Seam allowances are the extra fabric left around the seams to facilitate stitching. They provide the necessary margin for joining pieces together without compromising the garment's size and fit. Seam allowances also offer a bit of flexibility for alterations, which can be particularly useful in bespoke tailoring.
Additionally, notches and grainlines are marked on patterns to guide the construction process. Notches are small marks that help align different pattern pieces, ensuring precision during assembly. Grainlines indicate the fabric's direction, which is crucial for maintaining the garment's drape and flow.
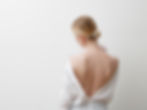
The Role of Pattern Cutters
Pattern cutters are essential artisans in the garment creation process, translating designers' imaginative sketches into precise, workable templates. These professionals blend artistic intuition with technical acumen, ensuring that each garment component aligns perfectly to create a cohesive, well-fitting piece. Their expertise extends to understanding the nuances of various fabrics and how they behave, ensuring the patterns they create account for the unique properties of each material.
Collaborating closely with designers, pattern cutters transform conceptual ideas into detailed patterns that guide the cutting of fabric. They must have a keen eye for detail and exceptional problem-solving skills, as even minor discrepancies can affect the fit and appearance of the final garment. Utilising their knowledge of garment construction, they meticulously draft and adjust patterns to ensure the final product meets the highest standards of quality and design fidelity.
Pattern cutters also play a crucial role in optimising fabric usage, contributing to the sustainability efforts within the fashion industry. By planning the layout of patterns efficiently, they minimise fabric waste, aligning with eco-friendly production practices. Whether using traditional manual methods or sophisticated digital tools, pattern cutters ensure that each piece of fabric is utilised to its fullest potential, maintaining the delicate balance between creativity and precision in the fashion world.
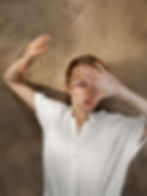
Tools and Materials for Manual Pattern Cutting
Manual pattern cutting requires an array of tools and materials to achieve precise and accurate results. Essential items include pattern paper, which is used to draft and trace the garment’s shapes. This paper is often durable and easy to work with, allowing for multiple adjustments and revisions.
Rulers and measuring tapes are crucial for obtaining exact measurements and ensuring all pattern pieces align correctly. French curves, a versatile tool, help create smooth, curved lines essential for various garment parts like armholes and necklines.
Sharp scissors are indispensable for cutting out pattern pieces cleanly and accurately. Some cutters prefer using rotary cutters, which can offer more precision for straight lines and intricate details. Pins are used to secure the pattern paper to the fabric, ensuring it remains in place during the cutting process.
Tracing wheels and tailor's chalk help transfer pattern markings onto fabric without causing damage. These markings are vital for aligning seams and other garment features during assembly. Additionally, pattern weights can be used to hold the pattern paper in place, providing stability without the need for pins.
These tools not only facilitate the pattern-cutting process but also allow for creativity and innovation in design, making manual pattern-cutting a rewarding and engaging practice for those passionate about garment creation.

Advantages of Manual Pattern Cutting
Manual pattern cutting offers a tactile and intimate approach to garment creation, enabling a level of detail and precision that can be particularly beneficial for bespoke designs. This hands-on method allows pattern cutters to directly manipulate materials, fostering a deeper understanding of fabric behaviour and how it can be shaped to achieve the desired fit and style.
One of the key advantages of manual pattern cutting is the flexibility it provides for custom adjustments. Pattern cutters can easily make on-the-spot modifications to accommodate unique body measurements or to experiment with innovative design elements. This adaptability is invaluable in creating one-of-a-kind pieces that stand out in the fashion market.
Additionally, the process encourages a strong sense of craftsmanship. Each pattern is meticulously drafted and cut, embodying the skill and artistry of the pattern cutter. This personal touch can enhance the uniqueness and authenticity of the final garment, appealing to customers who appreciate the dedication and expertise involved in its creation.
Moreover, manual pattern cutting can be more intuitive, allowing pattern cutters to draw directly on the fabric, making real-time decisions about shaping and fit. This immediate feedback loop can lead to quicker adjustments and refinements, ensuring that the final product meets the highest standards of quality and design fidelity.

Introduction to Digital Pattern Cutting
Digital pattern cutting harnesses the power of computer software to create and modify garment patterns with remarkable precision. This method revolutionises traditional pattern making by streamlining the design process and enhancing accuracy. Utilising specialised software, pattern cutters can draft intricate patterns, make swift alterations, and experiment with various designs without the constraints of physical materials.
One of the standout features of digital pattern cutting is its efficiency. Patterns can be generated and adjusted in a fraction of the time it takes using manual methods. This speed is particularly advantageous for designers working on tight deadlines or needing to make multiple revisions. Digital tools also enable precise replication of patterns, ensuring consistency across production runs.
The adaptability of digital pattern cutting is another significant benefit. It allows designers to simulate how different fabrics will behave, providing valuable insights before any fabric is cut. This capability can save both time and resources by identifying potential issues early in the design process. Additionally, digital patterns can be easily shared and stored, facilitating seamless collaboration among team members, even if they are geographically dispersed.
Digital pattern cutting aligns well with sustainable practices. By reducing the need for physical prototypes, it minimises material waste and contributes to eco-friendly fashion production. This method represents a blend of innovation and sustainability, pushing the boundaries of what’s possible in garment creation.

Benefits of Digital Pattern Cutting
Digital pattern cutting offers numerous advantages that make it an invaluable tool in modern garment production. One of the key benefits is its remarkable precision. By utilising specialised software, designers can create highly accurate patterns, reducing the likelihood of errors that can occur with manual methods. This precision is crucial, especially for complex designs that require meticulous attention to detail.
Efficiency is another significant benefit of digital pattern cutting. Patterns can be drafted, modified, and replicated swiftly, saving considerable time compared to traditional techniques. This efficiency is particularly beneficial for designers working under tight deadlines or needing to produce multiple iterations of a design quickly.
Digital pattern cutting also enhances collaboration. Patterns can be easily shared and adjusted in real time, facilitating seamless communication between team members, regardless of their location. This collaborative capability is essential for global fashion brands, ensuring consistency and coherence across different production sites.
Additionally, digital tools provide valuable insights into fabric behaviour before any material is cut. Designers can simulate how different fabrics will drape and react, allowing for informed decisions and adjustments early in the design process. This capability not only saves time and resources but also contributes to more sustainable production practices by reducing the need for physical prototypes.
Overall, digital pattern cutting represents a blend of innovation, efficiency, and sustainability, pushing the boundaries of what's possible in the fashion industry.

Comparing Manual and Digital Pattern Cutting
Manual and digital pattern cutting each offer unique advantages, catering to different needs in the fashion industry. Manual pattern cutting provides a tactile, hands-on approach, allowing for immediate adjustments and a deeper connection with the fabric. It fosters a sense of craftsmanship and is particularly valuable for bespoke designs and small-scale production. This method offers unparalleled flexibility, enabling on-the-spot customisations and intricate detailing.
Digital pattern cutting, on the other hand, harnesses technology to enhance precision and efficiency. Specialised software enables designers to draft, modify, and replicate patterns swiftly, making it ideal for large-scale production. This method reduces the likelihood of errors and facilitates seamless collaboration across geographically dispersed teams. Digital tools also offer valuable insights into fabric behaviour, helping designers make informed decisions early in the design process.
While manual pattern cutting excels in customisation and artistic expression, digital pattern cutting stands out for its speed, scalability, and precision. Integrating both methods can provide the best of both worlds, allowing for high-quality, bespoke clothing that meets diverse design needs while maintaining efficiency and consistency.

Sustainable Pattern Cutting Practices
Sustainable pattern cutting focuses on minimising waste and prioritising eco-friendly materials. Techniques such as zero-waste pattern cutting are designed to optimise fabric usage, ensuring that every inch of material is utilised effectively. This approach not only reduces waste but also maximises the efficiency of fabric consumption, a crucial consideration in sustainable fashion.
Digital pattern-cutting complements these efforts by significantly reducing the need for physical prototypes. By utilising computer software, designers can simulate the behaviour of different fabrics, allowing for precise adjustments and alterations before any material is cut. This method minimises waste and conserves resources, contributing to more environmentally responsible garment production.
Additionally, using organic and recycled materials in pattern cutting aligns with the principles of sustainability. These materials have a lower environmental impact compared to conventional fabrics, further enhancing the eco-friendly credentials of the garment production process. Incorporating sustainable practices in pattern cutting not only benefits the environment but also meets the growing consumer demand for ethically produced clothing.
By integrating these innovative techniques and materials, the fashion industry can move towards more sustainable and responsible production methods, fostering a greener future for garment manufacturing.
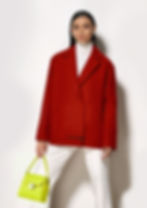
How Clothing Manufacturers UK Utilise Pattern Cutting
At Clothing Manufacturers UK, pattern cutting is an art form that combines traditional craftsmanship with modern technology to produce bespoke garments of exceptional quality. Our expert team uses both manual and digital techniques to bring each design to life, ensuring a perfect fit and finish for every piece.Â
Manual pattern cutting allows our artisans to meticulously craft each pattern by hand, providing the flexibility needed for custom adjustments and intricate details. This hands-on approach fosters a deep understanding of the fabric and its properties, enabling us to create garments that are not only aesthetically pleasing but also comfortable and durable.
On the digital side, we leverage advanced software to achieve unparalleled precision and efficiency. Digital pattern cutting enables us to make quick modifications, simulate fabric behaviour, and streamline the production process. This method is particularly valuable for complex designs and large-scale production, ensuring consistency and accuracy across multiple garments.
By integrating these two approaches, we can cater to a wide range of design needs, from unique, one-of-a-kind pieces to high-volume orders. Our commitment to ethical and sustainable practices is evident in our pattern-cutting techniques, which optimise fabric usage and minimise waste. This holistic approach ensures that every garment we produce meets our high standards of quality, sustainability, and style.

Getting Started with Pattern Cutting
Embarking on the journey of pattern cutting can be both exciting and rewarding. Begin by gathering essential tools such as pattern paper, rulers, French curves, and sharp scissors. These basics will equip you to start drafting and cutting simple patterns. For those leaning towards digital methods, investing in user-friendly software can be highly beneficial.
Practising with straightforward designs, like basic tops or skirts, allows you to grasp the fundamentals before progressing to more complex garments. Online resources, including tutorials and instructional videos, can provide step-by-step guidance and enhance your understanding of both manual and digital techniques. Additionally, enrolling in pattern cutting courses or workshops can offer hands-on experience and expert insights, accelerating your learning curve.
Joining online communities and forums can also be immensely helpful. Engaging with fellow beginners and experienced pattern cutters can offer support, feedback, and inspiration. Remember, patience and practice are key. As you refine your skills, you'll find greater confidence in your ability to transform design ideas into beautifully crafted garments.

FAQ
Q: What distinguishes manual pattern cutting from digital pattern cutting?Â
Manual pattern cutting involves hand-drawing and cutting patterns using tools such as rulers, scissors, and French curves. This method offers a tactile experience and allows for hands-on adjustments. Digital pattern cutting, on the other hand, uses specialised software to create and modify patterns with high precision and efficiency. It enables easy alterations and is particularly useful for complex designs and large-scale production.
Q: Why is pattern cutting essential in fashion?Â
Pattern cutting is vital because it directly influences how a garment fits and looks. Precise pattern cutting ensures that garments are comfortable, visually appealing, and structurally sound. It bridges the gap between a designer's vision and the final product, making it an indispensable part of garment production.
Q: How can pattern cutting be made sustainable?Â
Pattern cutting can be sustainable by optimising fabric usage through techniques like zero-waste pattern cutting. Additionally, using eco-friendly materials, such as organic or recycled fabrics, contributes to reducing the environmental impact. Digital pattern cutting also helps by minimising the need for physical prototypes, thereby conserving resources.
Q: Can beginners learn pattern cutting easily?Â
Yes, beginners can start with simple designs and gradually progress to more complex patterns. There are plenty of resources available, such as online tutorials, instructional videos, and workshops, which can provide step-by-step guidance. Practising regularly and engaging with online communities can also enhance learning and confidence in pattern-cutting skills.